Kickstarters and manufacturing can be tricky to setup and plan for. Have you thought through all the possibilities of what can happen with a Kickstarter campaign and manufacturing?
There is a lot to think about and plan for, especially for most people starting a Kickstarter campaign. Unless you’ve designed and worked on products through cradle to cradle product development, there are a few things you should pay attention to.
Manufacturing Lead Times
Sourcing manufacturers and then thinking that their lead times won’t change can be a huge pitfall. Lead times can change between the time you initially sourced the manufacturer and when you place your order. Lead times are usually only guaranteed if you order within a certain time limit.
Those time limits are typically 14-60 days depending on the manufacturer. Because of the potential long lead time between quoting and actual order time, this can cause issues.
Manufacturing lead times vary widely, especially in today's world. Controlling this is important to a successful crowdfunding campaign.
Ian Peterman, CEO Tweet
Quotes usually are good for 30 days and then they have to get requoted. This is typically because of lead times and them knowing what jobs they have over the next 30 days or so.
If someone else brings a huge order that takes up their floor to the point of pushing back any other future orders and you didn’t have a spot in their que, then your order may end up being delayed by days or even months.
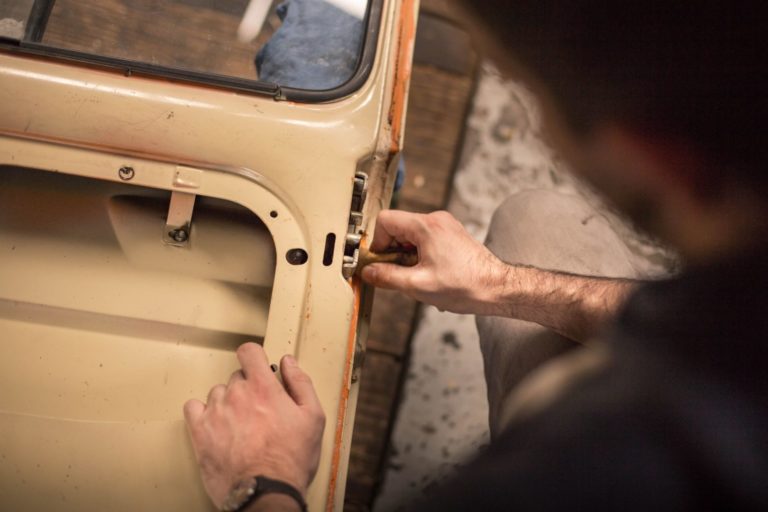
Product Vendor Failure
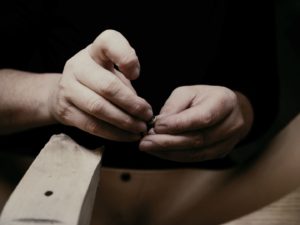
There are multiple ways failure can occur. The vendor could close its doors, which happens even to the huge companies. Production could start and quality issues can arise. Management can change unexpectedly and leave you with the a useless contract.
Companies pivot and stop offering certain services. Some of the issues with vendors can be mitigated by proper vendor vetting, however you can’t catch everything every time, especially if you don’t have an established relationship with the vendor.
Material Costs
You should know your current and future material costs before you even begin creating a crowdfunding campaign.
Ian Peterman, CEO Tweet
Material costs can sometimes swing in price drastically. We live in a global economy and pricing on materials change based on a number of things. Lower volumes always cost more than larger volumes.
How much is large depends on the manufacturing process. Manufacturing for a Kickstarter campaign typically doesn’t create enough volume to be considered high volume.

That being said, it can happen and planning for it just in case is worth the time, especially if you have goals for higher volumes shortly after your campaign ends. Manufacturing for a product based Kickstarter is different than other types of launches.
If you keep these things in mind, you can prepare for them. Managing your kickstarters and manufacturing is something anyone can do, but not always well. By working with a firm like us you can make ensure your Kickstarter delivery happens on time and outsource your sourcing.
Planning out your Kickstarter and manufacturing is the key to success. Back-up manufacturers, existing relationships, keeping your spot in production, and avoiding vendor failures are all things we can help with.
Your Next Steps
Want to turn your product into a business?
Sign up for our free tutorial and learn about our course
Related Conscious Design BLOG Posts
What is Design for Manufacturability?
Logically, you could figure out what Design for Manufacturability means in a broad sense. What does it really mean for you and your product? Design for Manufacturability, or DFM for short, is where Design meets Production. The DFM process takes a design and produces a final design that can be manufactured properly, and at the desired cost. This step is often skipped by those developing their first product. They end up costing more. Investing more on time and money than it should. We’ll go over some of what DFM does for your product and why it is a very key component to developing a great product. Manufacturability This is the first step in DFM. An engineer or designer takes a design and reviews it to ensure the product can be manufactured as efficiently and effectively as possible. Draft angles for injection molded parts, machinable areas for CNC, stacking tolerances, fit checks, and many more items are part of this DFM checklist. BLANK Ian Peterman, CEO Tweet Costing This is where things can get interesting, such as actually increasing part count, decreasing reusable parts, etc may be required to put a product into a certain price window. Costing looks at every cost of a product, from hardware selections, country of production, materials, and how each part needs to be made. A Sourcing Agent is closely tied into this part of the process, and works with the designer through this process. Part Count BLANK Ian Peterman, CEO Tweet How many parts does it take to make your product? I’ve worked on products ranging from just one to the thousands. A part count is a balancing act, sometimes you can make 4 parts into 1, but the cost would be 10 times greater. The part count is an easy way to estimate product complexity, assembly costs, et. Usually more is more expensive, and so a lot of work can be done to decrease the part count, make assembly easier, and take less time. Reuse and Replacement For those businesses who are sustainably minded, which every business should be, designing a product for reuse is something that happens in the DFM stage. Which components can be reused, which need to be replaced, even what parts can be recycled or not are also influence in the DFM process. Material and Finish blank Ian Peterman, CEO Tweet DFM also looks at what materials and finishes are used in a product. Sometimes a material might be chosen that doesn’t work well with a certain manufacturing process or is extra expensive. Changing a material, or finish can change the perceived quality, actual quality, and the cost of a product drastically. Lead time is also influenced by finishes as they add extra time to production. Lead Time A lead time of a product determines how quickly a business can turn its manufacturing investment into a profit. If it takes 10 weeks to produce a product, that means a business is going to wait at least 10 weeks before it gets paid. Decreasing lead time also falls within the DFM process. Shorter lead times mean quicker product turnaround, as well as usually less costly. Through selecting processes, materials, and finishes, the DFM process can save businesses from having long costly lead times on their products. Your Next Steps manufacturing Products Kickstarters and Manufacturing: What to Pay Attention to manufacturability Conscious Design Choosing a Manufacturer choose a manufacturer Related Conscious Design BLOG Posts Author Mr. Peterman View all posts
2 Tools you Should use with Your Developer
When working with a product developer, there are two types of programs you should be familiar with. While there are many options for each one, these two types of programs will help with communication between you and your developer. The first one is one you probably don’t have unless you work with people in 3D often, the other is common, but I’ve run into clients who didn’t use or were unfamiliar with them as well, mostly old school small businesses. 3D viewer You will need this for pretty much any physical product development anymore. While we might start out with sketches and PDFs, which you can make a 3D PDF too now, we quickly move into 3D now. Being able to view your developer’s 3D model from every angle, cross-sectioned, and hiding parts is essential to the review process. Many mid to high-end CAD packages have viewers that work with their software. It is also sometimes a good idea to ask your developer about simple CAD packages that are free/cheap that can open CAD files for you to review. We use SolidWorks primarily, and eDrawings is its free viewer. BLANK Ian Peterman, CEO Tweet File-Sharing Most people think of getting files from the developer, but it’s really a two-way street. You will want to send your initial documents to your developer, as well as feedback and other information in an easy way. Often these files are much larger than what an email can handle, so a file-sharing tool or service best meets these needs. There are many options here, far more than for the 3D viewers, so there is something for everyone. Setting up a shared “folder” with your developer where all files go to will keep things easy and straightforward for both of you and avoid losing any emails with files that you can’t find anymore. For this, we use Google Drive and Dropbox primarily. Talk with your developer, see what programs they use, and make sure everything is compatible. Good developers will set up file sharing through their preferred service, they pay for larger storage and more features than you would probably want to pay for. These tools, in addition to all the other programs and services we all use on an average day, will ensure you and your developer are able to communicate effectively. Your Next Steps Developing Smart Products What do you bring to a developer? Develop a Smart Product Modern Tools Tools of the Design World: Blender Blender Related Conscious Design BLOG Posts Author Mr. Peterman View all posts
Top 5 Ways to Maximize your Developers Potential
These are the top 5 things that have made projects easier to accomplish and more successful. Make sure you have these with your project to be as successful as possible.